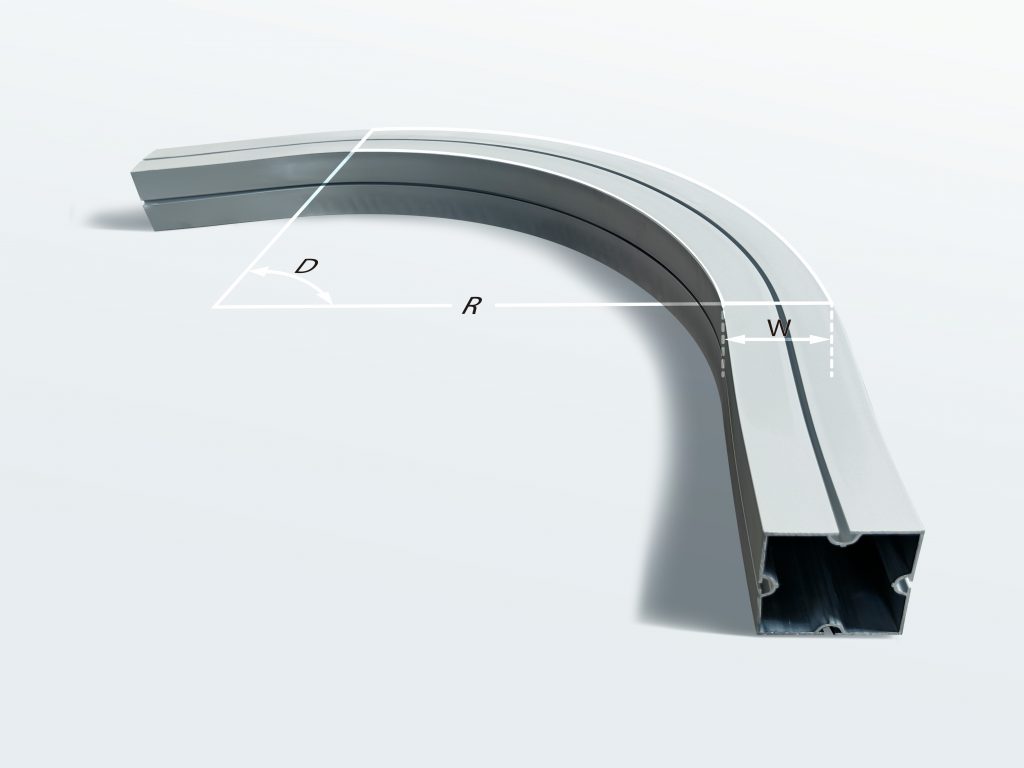
This calculator helps you estimate the minimum aluminum profile bending radius for common aluminum extrusion alloys such as 6061 and 6063, across their T4, T5, and T6 tempers. By entering the profile width and selecting the bending direction, you’ll get three reference radii based on varying elongation values.
These results are for reference only and reflect typical material behavior. In real-world bending, many profiles can be successfully formed using the maximum elongation value—producing excellent results without failure. However, actual performance depends on your material supplier’s specs, so always verify before production.
Use this tool during early design to avoid excessive trial-and-error and minimize scrap risk.
Aluminum Extrusion Minimum Bend Radius Calculator
Calculation Results of the Minimum Bending Radius of Aluminum Extrusion Profiles
Temper | Allowed Elongation | Minimum Safe Inner Radius (mm) | ||
---|---|---|---|---|
Conservative (Min ε εmin=12%) |
Recommended (Avg ε εavg=15%) |
Risky (Max ε εmax=18%) |
||
T4 | – | – | – | – |
T5 | – | – | – | – |
T6 | – | – | – | – |
Note on Elongation and Bending Radius Calculation:
This calculator provides estimated minimum bending radius values based on the elongation range of aluminum alloys 6061 and 6063 in their T4, T5, and T6 tempers. For example, 6063-T4 typically has an elongation between 12% and 18%, so we offer bending radius outputs for 12%, 15%, and 18% to reflect this range.
In actual production, bending at the higher end of the elongation range often produces better results and is widely practiced(For example, 18% of 6063-T4 ). However, please be aware that elongation values can vary depending on the extrusion manufacturer, specific profile design, and quality control. Always refer to the material test report (MTR) or consult your supplier for precise data before finalizing a bending process.
These values are for reference only. For critical applications, we strongly recommend validating the material’s properties through actual testing.
Material Properties:
Alloy-Temper | Tensile Strength (UTS) | Yield Strength (YS) | Elongation (%) | Characteristics |
---|
Primary Sources for Elongation Data
- “Aluminum Standards and Data” — Published by the Aluminum Association (USA) • This is the most widely cited aluminum alloy reference worldwide, detailing the mechanical property ranges of 6061 and 6063 in various heat-treated conditions. • It includes tensile strength (UTS), yield strength (YS), elongation, and more.
- ASTM B221 Standard — Standard Specification for Aluminum and Aluminum-Alloy Extruded Bars, Rods, Wire, Profiles, and Tubes • Defines the minimum mechanical properties for 6061 and 6063 in T4, T5, and T6 tempers.
- Metals Handbook — Published by ASM International • Contains measured and statistically compiled physical and mechanical properties of 6061 and 6063 aluminum alloys.
🔧 Need More Bending Geometry Tools?
For enhanced precision in bending design and machine setup, try our online bending geometry calculators:
- Arc Length Calculator – Calculate arc length from radius and angle.
- Angle Calculator – Find bending angle from arc length and radius.
- Radius Calculator – Work backward from arc length and angle.
👉 These tools simplify bending planning, reduce errors, and boost productivity.
Bending Calculator Suite: Arc• Angle • Radius
Precision Arc Length • Bend Angle • Radius Calculations: To support precise design and operation in aluminum profile bending, this page provides six practical online calculators. These tools enable quick calculations of arc length, bending angle, radius, sagitta, and ovality based on your input parameters—helping you streamline production and ensure bending accuracy.
Function Overview
- Arc Length Calculator • Calculates the arc length from a given radius and central angle. • Helps estimate material length for efficient cutting and nesting.
- Angle Calculator • Computes bending angle from input radius and arc length. • Assists in setting accurate bending machine parameters.
- Radius Calculator • Determines bending radius based on known arc length and angle. • Useful for designing complex curved profiles precisely.
- Mid-Ordinate (Sagitta) Calculator • Calculates the sagitta (mid-ordinate) — the height of the arc — from radius and chord length. • Important for understanding vertical displacement in bent profiles.
- Radius from Chord & Mid-Ordinate Calculator • Derives the radius using chord length and sagitta values. • Supports verification and correction of bending geometry.
- Ovality Calculator • Measures the ovality (deviation from circularity) of profiles. • Critical for quality control in bending round or oval sections.
💡 Use these calculators together to enhance accuracy, reduce errors, and optimize your aluminum profile bending process.
Bending Arc Length, Degree, and Radius Calculator
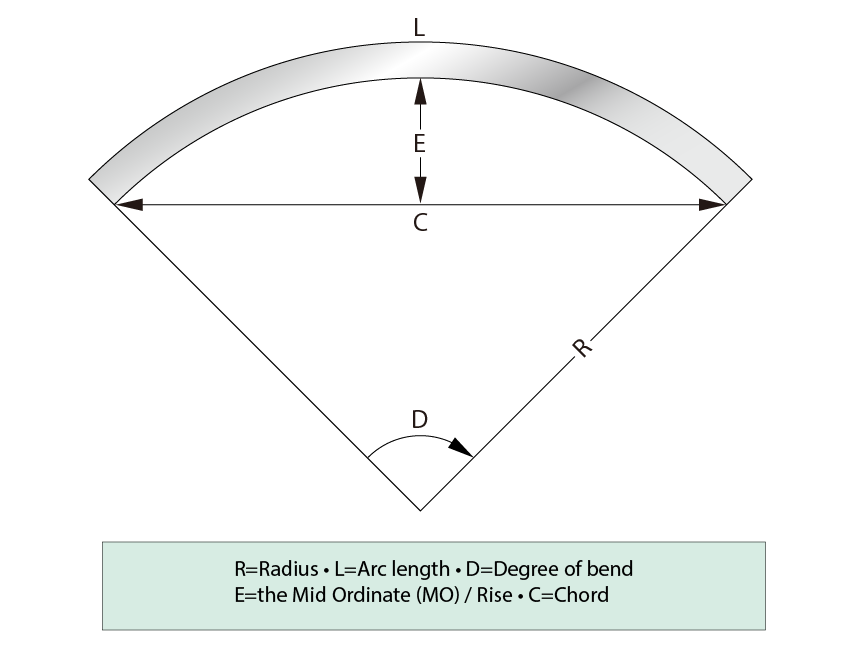
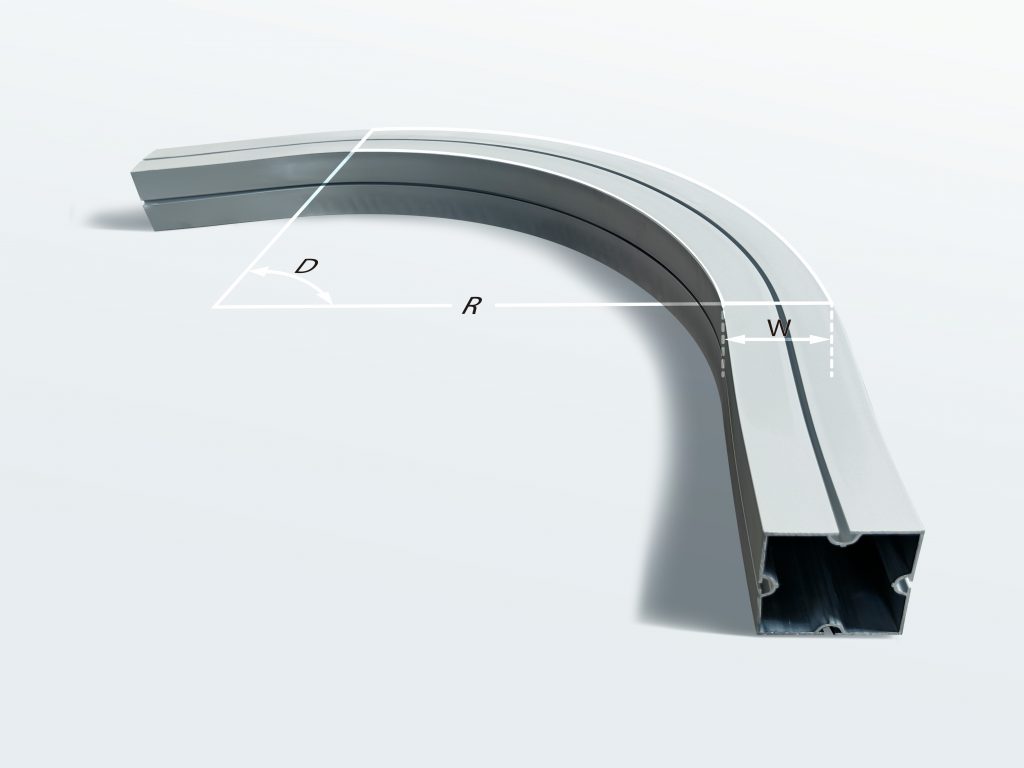
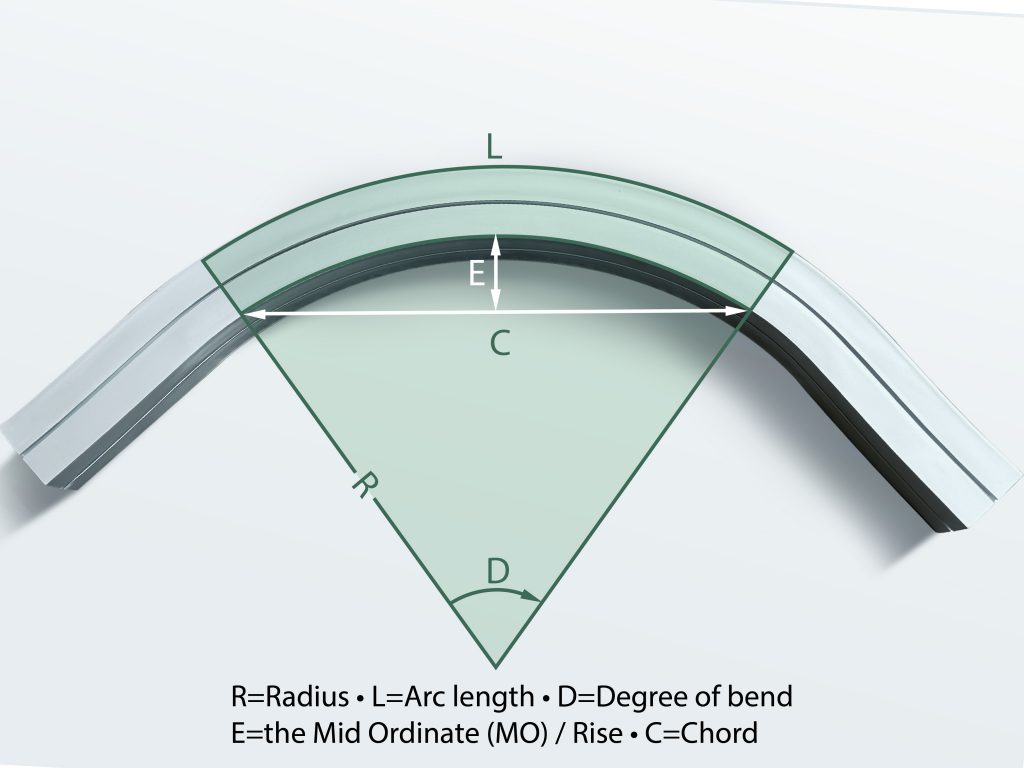
Arc Length Calculator
Angle Calculator
Radius Calculator
Mid-Ordinate (Sagitta) Calculator
Radius from Chord & Mid-Ordinate
Pipe or Tube Ovality Calculator
How to Use
- Enter any two parameters and click the “Calculate” button to get the third value.
- Switch between units (mm/inch) to suit regional preferences.
- Use the “Clear” button to quickly reset all inputs for repeated testing.
Recommended Tool
Want to find out the minimum bendable radius based on your profile size and material type?
👉 Try our Aluminum Profile Bending Radius Calculator — designed to estimate safe bending limits for different aluminum profiles and alloys.
💡 Need to estimate aluminum profile weight during bending design? Try our Online Aluminum Profile Weight Calculator — ideal for quickly calculating the weight of aluminum extrusions such as U-shaped channels and custom profiles. Simply input dimensions and alloy type to get precise results for production planning.
Ovality Calculator – Quickly Check Pipe or Tube Roundness
This tool helps you calculate ovality, a measure of how much a pipe or tube deviates from a perfect circle.
Just enter the maximum and minimum diameters of the cross-section, and the calculator provides the ovality percentage.
Why It Matters:
- ✅ Ensures dimensional accuracy in bending and forming
- ✅ Helps detect out-of-tolerance or defective materials
- ✅ Useful for QA checks during aluminum and steel profile processing
Formula Used:
Ovality (%) = (Max Diameter - Min Diameter) ÷ Nominal Diameter × 100
🛠️ Tip: Use this before bending to confirm material roundness and prevent deformation or profile cracking.
Role in Aluminum Profile Bending
- Accurately predict arc and developed lengths to help technicians prepare materials and reduce waste.
- Optimize bending program settings by aligning inputs with the bending machine for better consistency.
- Boost design efficiency by enabling designers to quickly verify if a structure meets bending requirements.
These calculator tools will become your indispensable assistants in aluminum profile bending design and production!