Aluminum Tube Bending
Bending aluminum tubing offers extensive applications, especially in scenarios that combine aesthetic design with structural functionality. It presents challenges like material springback, risk of cracking, and maintaining cross-sectional integrity.
Aluminum Tubing
Aluminum tubing typically refers to square aluminum tubes, while aluminum pipe usually refers to round pipes.
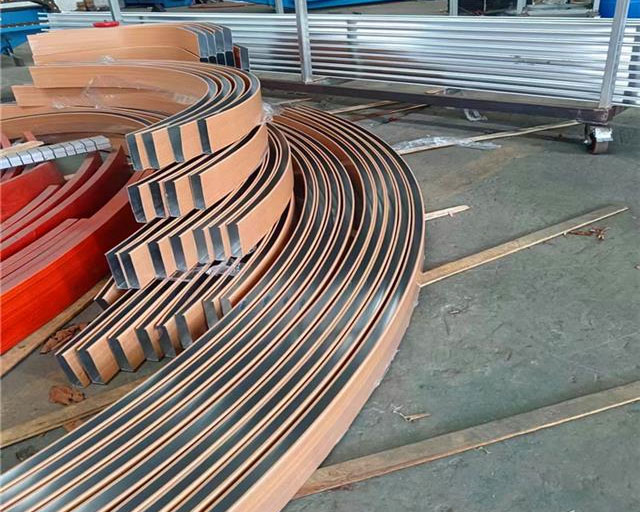
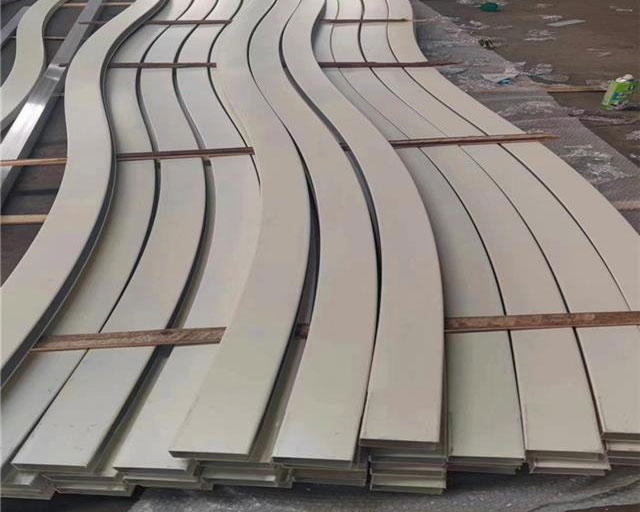
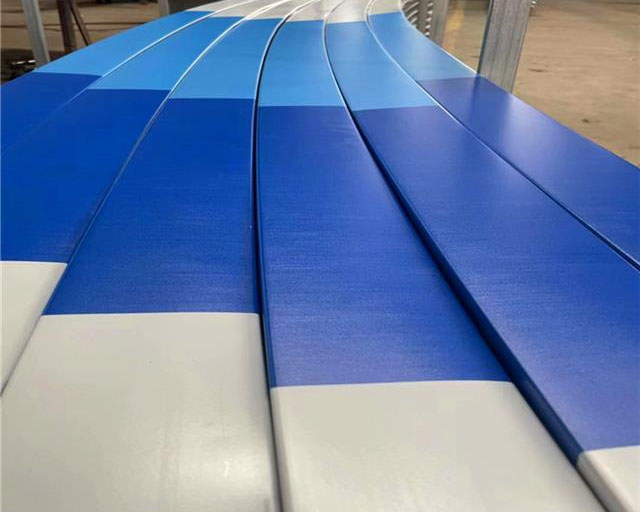
Aluminum tubing is a square or rectangular hollow tube made from aluminum alloys. It is commonly classified by specifications such as wall thickness, side length, and material. Popular materials include aluminum alloys like 6061 and 6063, with wall thickness ranging from 0.5mm to several millimeters, customizable as needed. Widely used in construction, industrial, and decorative fields, aluminum tubing is highly valued for its lightweight, high strength, and corrosion resistance.
How to Bend Aluminum Tubing Without Kinking? From Filler to Hollow
There are several techniques for bending aluminum tubing without kinking, ensuring smooth curves and structural integrity. Without proper methods, tubing can easily wrinkle, collapse, or deform. Filler bending techniques provide internal support to prevent kinking, making them ideal for tight-radius bends and thin-walled tubing.
Filler Bending
Filler bending involves filling the aluminum tubing with materials like mandrels, sand, or polyethylene before bending. This method prevents kinking, collapse, or wrinkling, ensuring a smooth and precise bend. After bending, the filler is removed, leaving the tubing intact and free from deformation.
Sand-Filled Bending: Dry sand supports small-radius bends or thin-walled tubing, reducing the risk of kinking.
Mandrel Bending: A metal mandrel reinforces the inner wall, preventing wrinkles or collapse—ideal for high-precision bends without kinking.
Flexible Filler Bending: Special flexible materials, like resin beads or bending agents, provide even support, ensuring consistent bending results without kinking.
- Advantages: Prevents kinking, reduces springback, enhances precision, and maintains an accurate inner radius.
- Disadvantages: Stretching and thinning can occur at the bend due to tensile forces, leading to longitudinal shrinkage and reduced wall thickness.
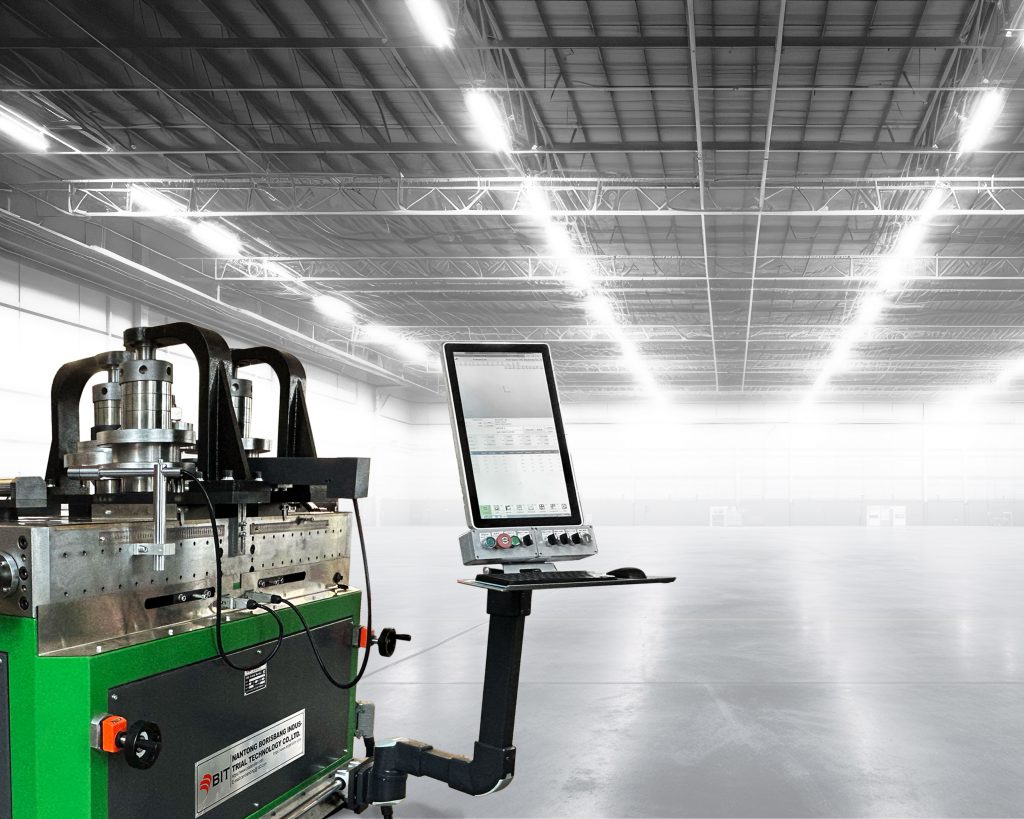
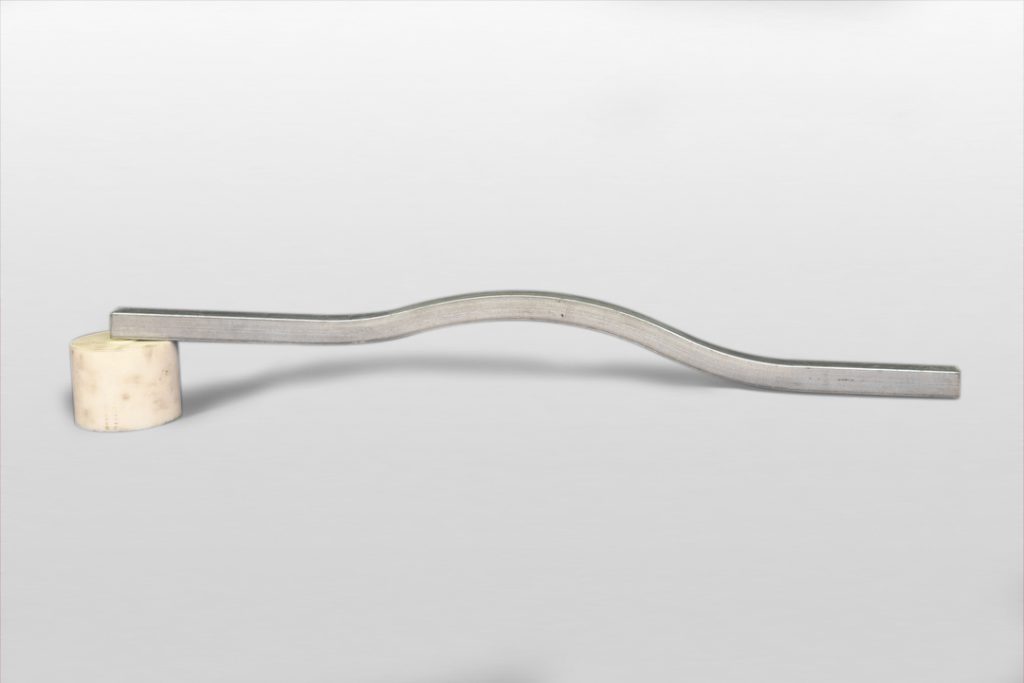
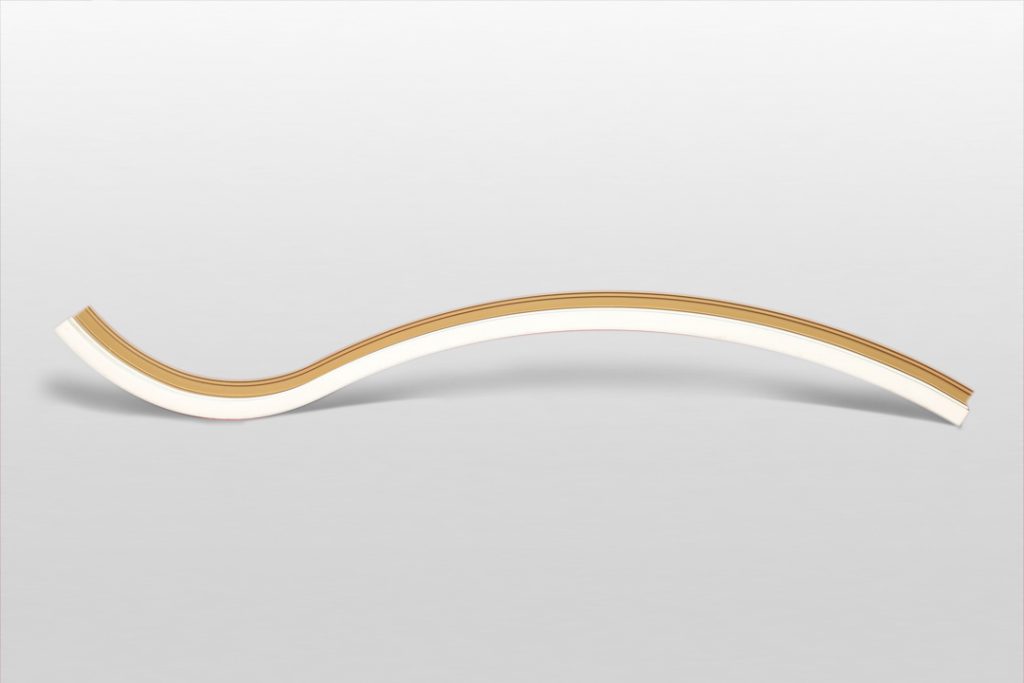
Filler bending is an effective way to enhance precision and prevent defects in bending aluminum tubing, especially for demanding applications. Choosing the right filler method depends on the tubing’s wall thickness, bend radius, and required accuracy.
Hollow Bending (Non-Filled Bending)
Hollow bending applies direct bending force to hollow aluminum tubing without any internal fillers. It is suitable for larger-radius bends or tubing with sufficient wall thickness. It forms a bend moment by contacting the tube’s outer wall with external force. Compression effects elongate the longitudinal bending line, while metal at the bend compresses and thickens, leading to the compression/thickening effect.
Advantages: Suitable for edge bending when filler bending isn’t feasible, such as simultaneous bending and trimming of rectangular tubing’s top and side edges. Hollow bending can also bend inner corner radii without causing wall rupture.
Disadvantages: During simultaneous top/side hollow bending (roll bending), excessive forming force can cause instability, internal concavity at the edges, and affect machine stability and forming quality.
Bending Conditions for Aluminum Tubing
- Cold Bending Conditions:
Cold bending is performed at room temperature and is ideal for medium wall thickness and large-radius bends. It is simple, cost-effective, but may require angle adjustments due to material elasticity and springback. Thin-walled tubing or small-radius bends risk wrinkling or collapse, which can be mitigated by optimizing molds or using fillers. - Hot Bending Conditions:
Hot bending heats the tubing to enhance ductility, suitable for high-strength or small-radius bends. This reduces cracking and deformation but requires precise control of temperature and time to avoid overheating, which can degrade material properties.
Filler bending provides internal support and performs well under cold bending conditions for cost efficiency. In hot bending, it prevents cracking during tight-radius bends. Hollow bending is ideal for large-radius and simple shapes, with cold bending being economical. For small-radius complex curves or high-strength materials, hot bending ensures superior precision and quality.
There are many methods for bending aluminum tubing. Based on the forming approach, it includes roll bending, stretch bending, push bending, rotary bending, manual bending, and freeform bending. Depending on mold usage, bending aluminum tubing can be classified into mold bending and mold-free bending. By the use of a mandrel, methods are divided into mandrel bending and non-mandrel bending. Additionally, considering whether heating is applied, it can be categorized into cold bending and hot bending.
Cold Bending Methods in Bending Aluminum Tubing
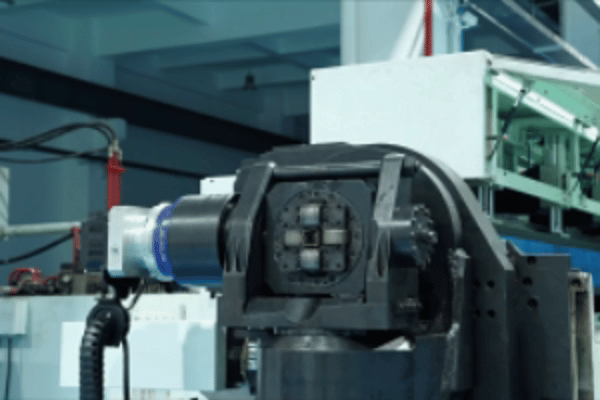
- Roll bending involves passing aluminum tubing through a set of rollers to achieve a curved shape. It is commonly used for producing large-radius bends and works well for long lengths of material.
- Stretch bending allows for both small-radius and large-radius bends and is commonly applied in industries like aerospace and automotive for parts that require a high level of accuracy and strength.
- Rotary bending uses a rotating die to bend the aluminum tubing around a fixed axis. This method offers high precision and is commonly used for tight-radius bends in tubing applications.
- Manual bending is done by hand using tools such as handheld benders or jigs. It is typically used for small-scale production or custom, one-off bends, and is suited for flexible, low-volume work.
- Freeform Bending allows for the bending of tubing into complex, irregular shapes without the use of fixed molds or tooling.
4 Types of Cold Bending Machines for Bending Aluminum Tubing
Several forming machines are suitable for bending aluminum tubing, depending on the section type—solid, open, or hollow—the available support tooling, and the alloy and temper. Tubing is the most commonly bent aluminum form, and four main bending methods are used:
- Three-Roll Bender: A central moveable roller gradually depresses the tube until the desired radius is achieved.
- Three-Point Bender: Operates similarly, applying force either gradually or by impact.
- Roll and Point Bending: Ideal for robust sections; wrap and mandrel benders help minimize buckling and enable tighter radii.
- Stretch Forming: Places the tubing under tension and wraps it around a former, reducing compression failure.
Point: For bending aluminum tubing, drawn tubing is preferred for its tight tolerances and superior mechanical properties. Its uniform structure allows for more consistent bending than extruded tubing. Softer tempers are recommended for complex shapes to achieve optimal bending results.
Conclusion
Bending aluminum tubing requires the right method to ensure accuracy, durability, and a smooth finish. For small-radius or thin-walled tubing, filler bending techniques like mandrel or sand-filled bending prevent kinking and deformation. Hollow bending is more suitable for larger-radius bends and applications where internal fillers are unnecessary. Cold bending offers cost efficiency and is widely used in construction and general fabrication, while hot bending enhances ductility for high-strength alloys or tight-radius curves.
Choosing the appropriate bending technique depends on material properties, bend radius, and production requirements. By leveraging precise bending methods—whether roll bending for gradual curves, rotary bending for tight-radius bends, or stretch forming for high-precision applications—manufacturers can ensure high-quality, structurally sound aluminum tubing for industries ranging from automotive to aerospace and beyond.