Effortless Bending of Complex Aluminum Extrusions
Aluminum Profile Bending
At BIT, the world curves with precision — perfect arcs and elegant shapes, imagined and engineered.
Aluminum profile bending, also known as aluminum extrusion bending, refers to the precise forming of curved arcs from aluminum extrusion profiles. The aluminum profile bending process is widely used in architectural systems such as windows, doors, and curtain walls, as well as in LED lighting, industrial automation, automotive, rail transit, aerospace, medical equipment, and display framing applications.
Aluminum Profile Bending has become a crucial process in modern manufacturing, thanks to the material’s light weight, corrosion resistance, and ease of processing. Aluminum profiles offer high structural strength and rigidity, save space, and enhance design flexibility—making them widely used in architecture, transportation, and industrial applications.
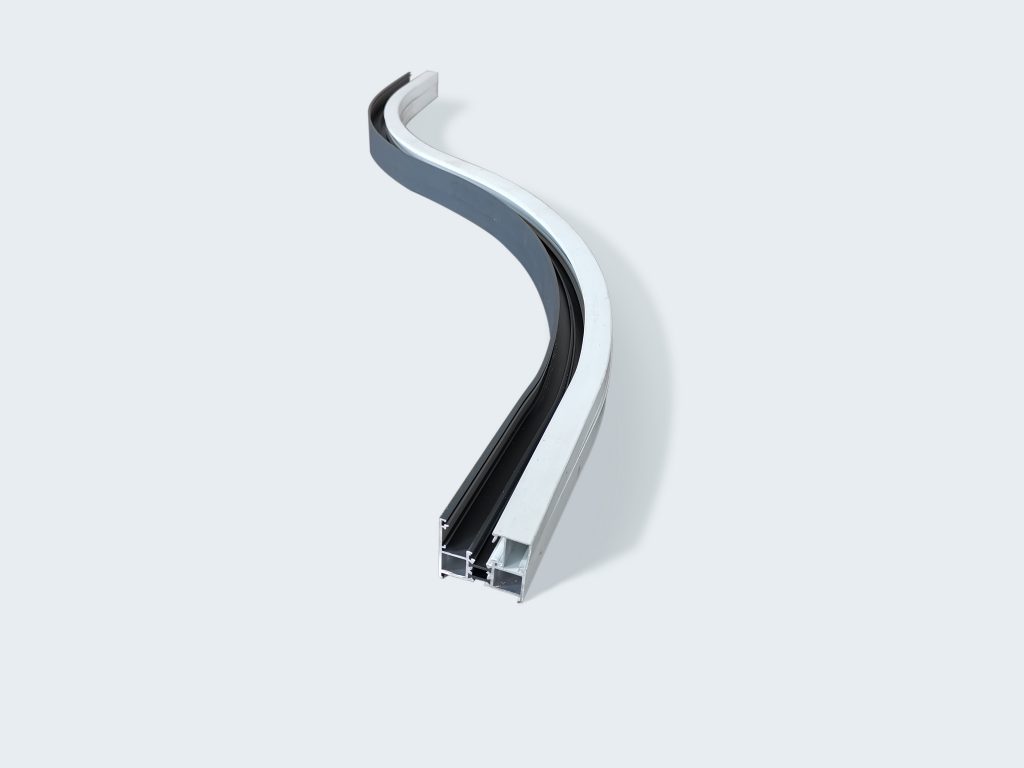
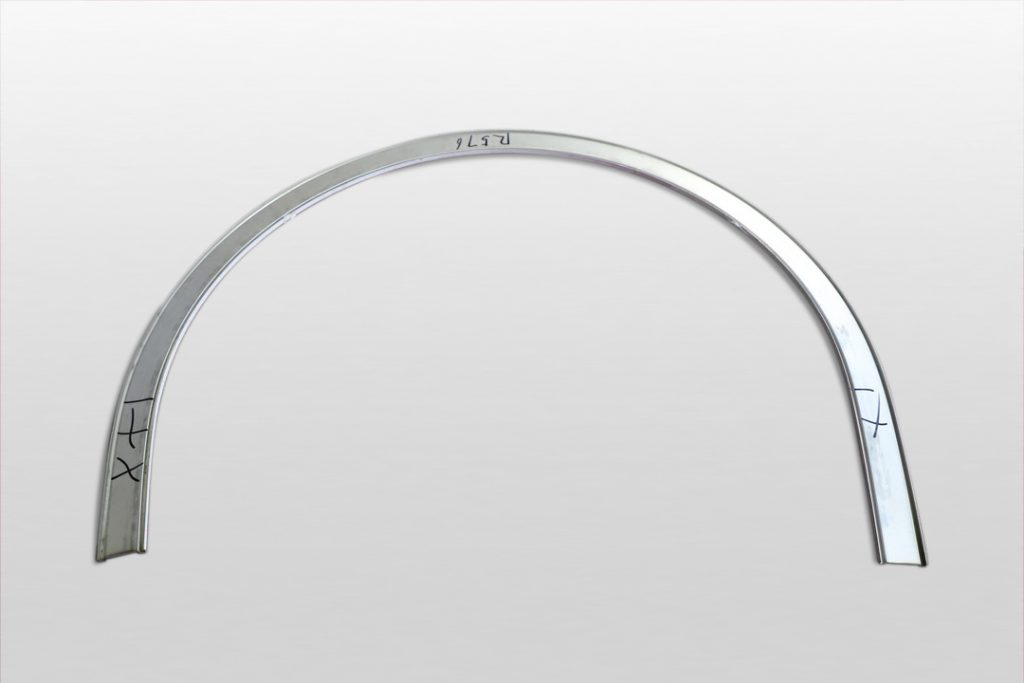
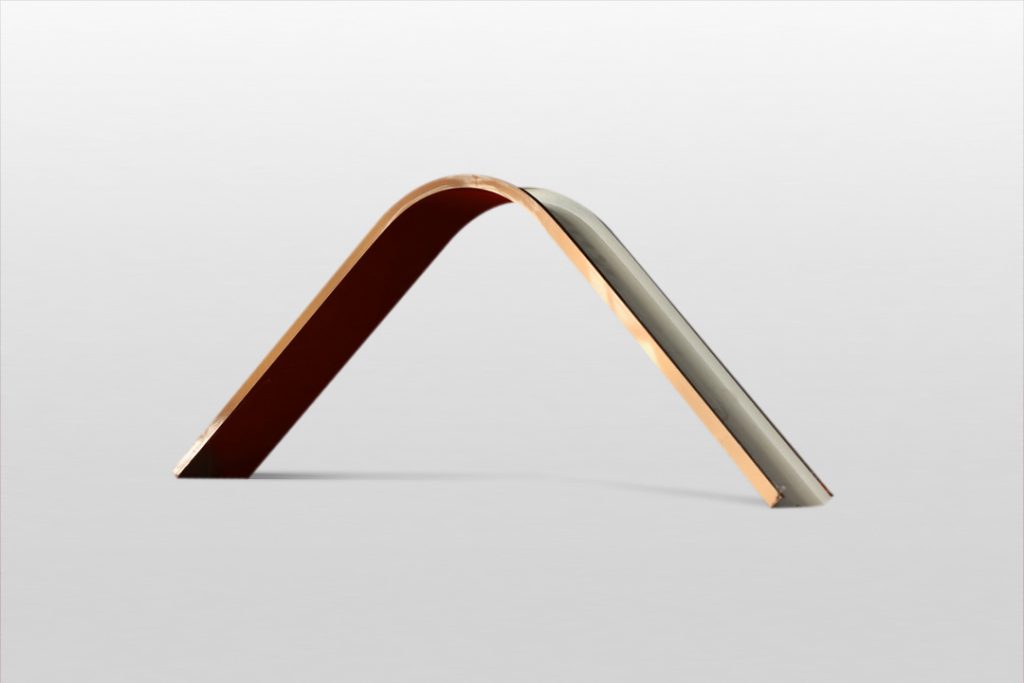
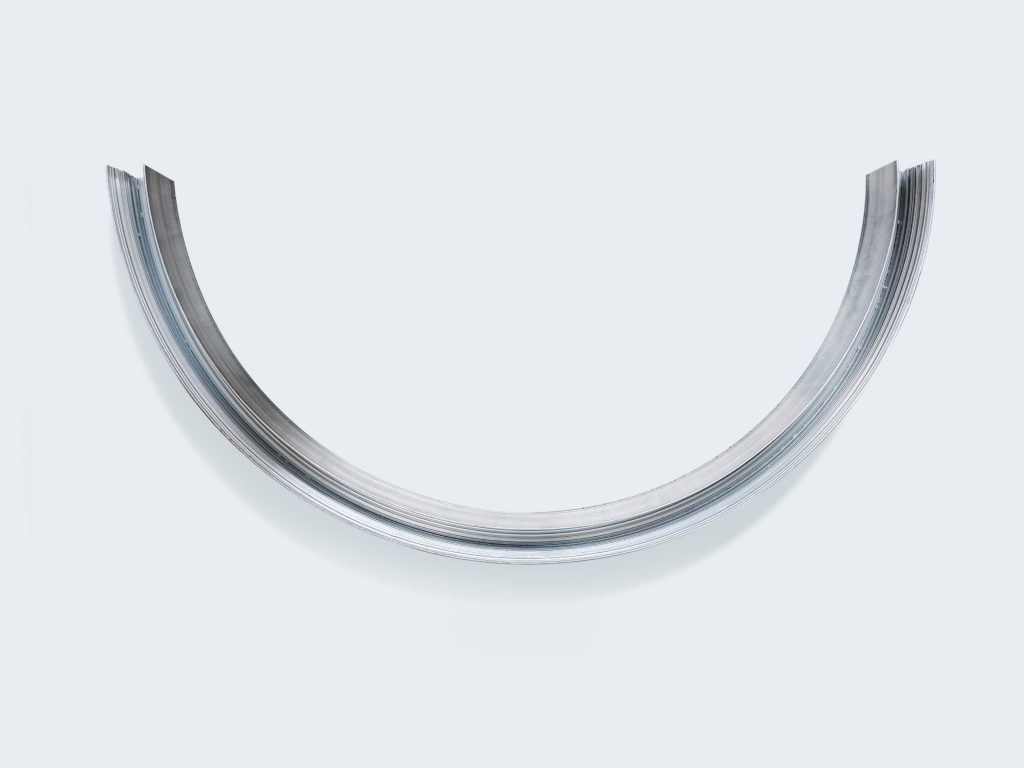
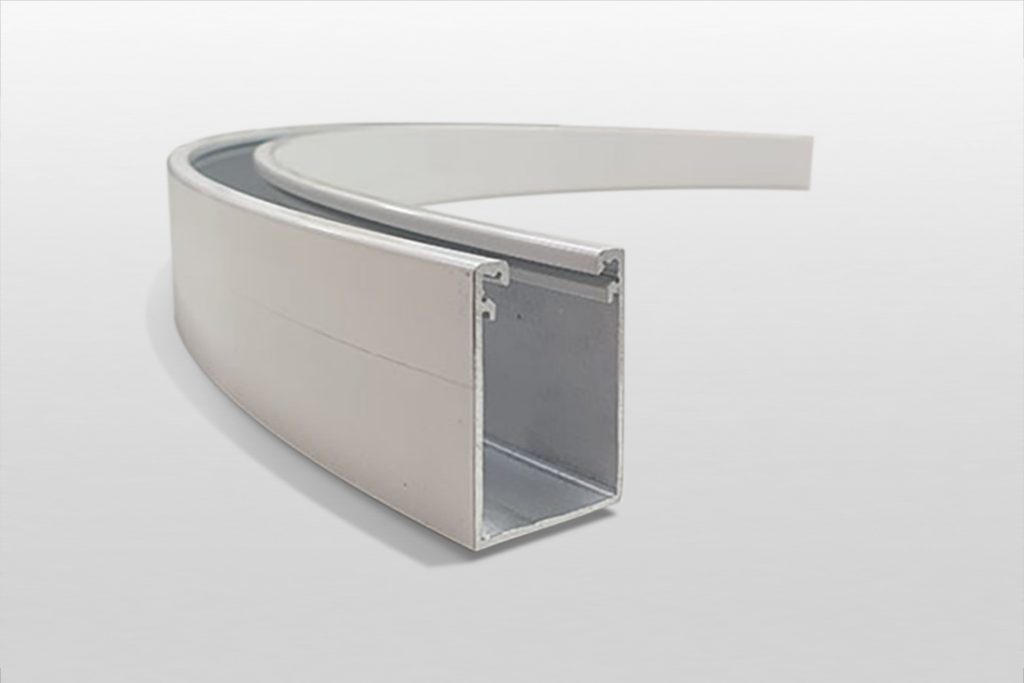
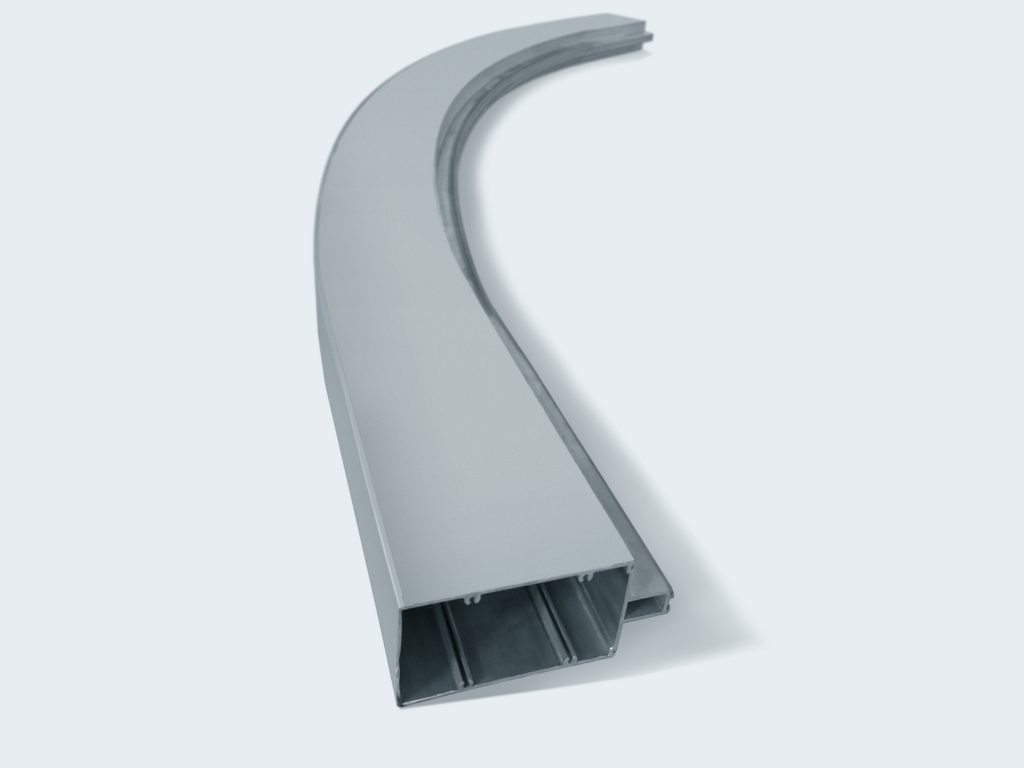
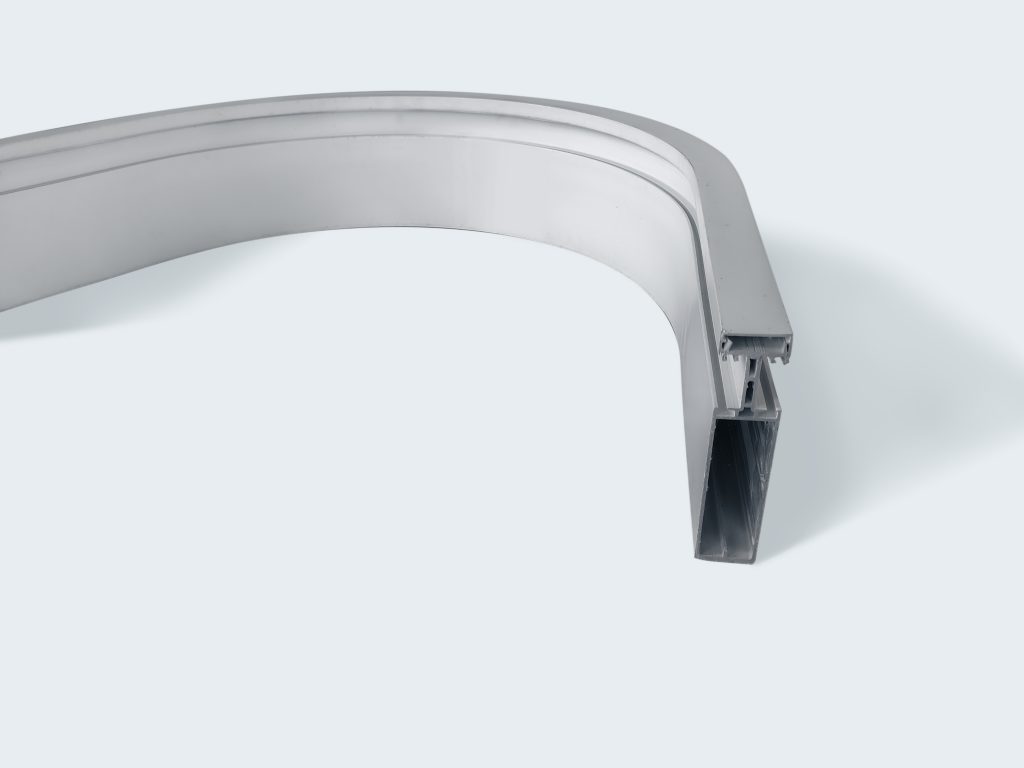
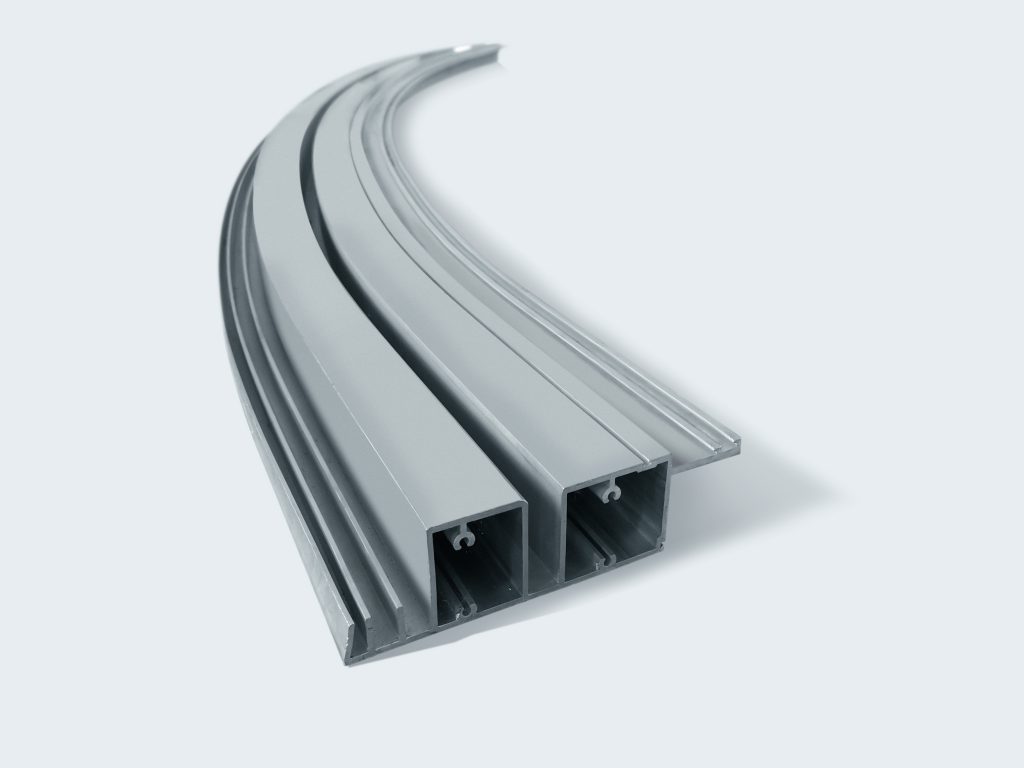
To meet increasingly complex and customized design needs, aluminum profiles often require precision bending. Well-designed and effectively bent aluminum profiles create seamless connections within structures., enhancing both performance and aesthetics.
Compared to steel, aluminum extrusions is more suitable for cold bending(roll bending or stretch forming). It allows for smaller bending radii and superior surface quality, making it ideal for forming complex curves and shapes. High-quality Aluminum Profile Bending process must meet key criteria:
• High arc accuracy
• Stable springback
• Consistent dimensions across parts
• Multi-radius and variable-curvature bending capabilities
Application of Aluminum Profile Bending
Aluminum profile bending involves stretching and compression, which can cause cross-sectional deformation and surface damage. Cross-sectional deformation can make the part impossible to install, while surface defects, such as wrinkles, not only compromise aesthetics but can also negatively impact performance.
With the expertise of BIT’s bending engineers and the precise tool design of our PBA aluminum bending machines, we deliver perfect aluminum bending every time.
Mirror Frame Aluminum Bending
Among various aluminum profile bending applications, mirror frame aluminum bending is one of the most complex. Although the equipment required is compact, the profile shapes are highly varied—including circles, ellipses, racetracks, rounded polygons, pentagrams, and other irregular forms. To achieve precise and consistent results, a computer-controlled CNC system is essential.
At the same time, due to the small cross-section and high flexibility of these profiles, issues such as cracking, deformation, or wrinkling are less likely to occur. This makes it one of the easiest bending processes to control, typically using roll bending technology.
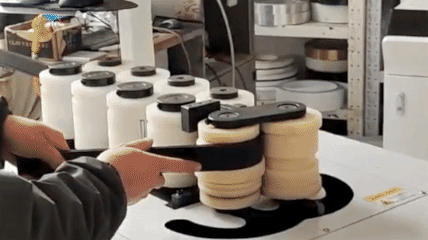
Bending LED Light Aluminium Extrusion Profiles
Bending LED lighting extrusions poses a significant challenge due to their thin walls and highly asymmetric design.
These profiles are typically U-shaped channels with long, slender side legs and minimal wall thickness to reduce ceiling load. However, during bending, this asymmetry generates substantial torsional forces, often causing the side legs to twist inward toward the centerline.
To improve bending stability, we recommend optimizing the profile design in the early stages—minimizing asymmetry and increasing the bending radius where possible(In the animation on the right, a temporary connecting structure was added to the LED aluminum extrusion profile before bending; the manufacturer removed it after bending.). For more difficult bends, T4 temper is strongly advised, followed by artificial aging to restore strength. For larger radius applications, T5 or even T6 tempers may also be used. Red More: Bending LED Light Extrusion Profiles
PBA Aluminum profile bending machine has helped clients successfully bend various LED light extrusions while preserving profile integrity and visual quality.
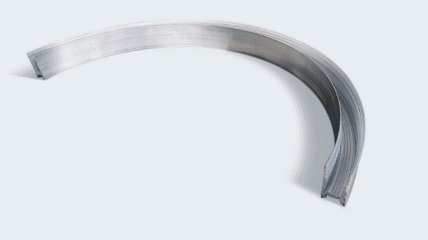
Bending Aluminium Window Frames
Bending aluminum window frame profiles is one of the most common—and technically demanding—applications in aluminum profile forming.
At the design stage, it’s essential to consider the profile’s cross-sectional shape, the required bending radius, and whether the surface is anodized or coated. Surface treatment affects not only appearance but also the complexity of protection during bending.
To ensure optimal results, profiles are typically bent in the T5 temper. If necessary, T4 temper can be used with post-bending artificial aging. If the material hardness is too high, cracking may occur during bending; if too soft, surface wrinkling or cross-sectional deformation may result.
With the right combination of equipment, tooling, and proven processes like roll bending or stretch bending, profiles can be formed precisely while maintaining their structural shape and surface integrity—efficiently and without damage. Read More: Aluminium Window Frames Bending
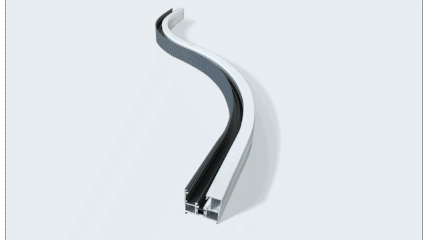
Bending Aluminium Curtain Wall
Curtain Walls Aluminium façade components of all types can be bent.
Curtain wall profiles are typically designed with multi-chamber structures, large cross-sections, and complex contours, and are finished with high-quality surface treatments such as anodizing or powder coating. During bending, they are highly susceptible to cracking, cross-sectional deformation, and surface damage or scratching.
Bending Methods:
Roll Bending: Ideal for long components with large radii; offers high efficiency.
Stretch Bending: Controls springback through applied tension; suitable for small-radius and complex-curved curtain wall profiles with strict appearance requirements. A recommended minimum bending radius chart is for roll bending applications. Online Bending Radius Calculator: 👉 Try the calculator now
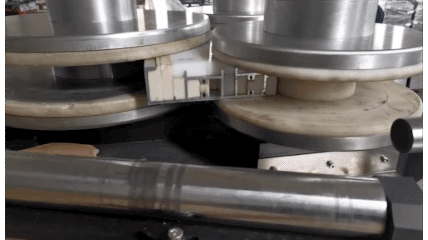
Flexible Conveyor Aluminum Profile Bending Application
Our PBA aluminum profile bending machine solutions are widely used in flexible conveyor systems. Horizontal bends are typically formed by joining two half-bent profiles with precision clamps. For vertical applications, sliding bends are shaped from a single solid profile to ensure strength and smooth operation.
With the PBA, complex layouts become simple to implement, improving design freedom and operational efficiency.
Stretch Forming and Roll Bending for the Automotive Industry
Stretch forming is a precision forming process widely used in the automotive industry to shape aluminum profiles into complex, three-dimensional curves. Stretch bending ensures smooth, wrinkle-free surfaces—ideal for exterior trim, window frames, roof rails, and bumper components.
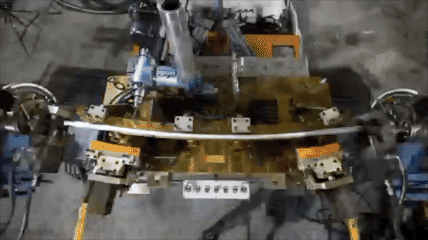
Performance of Bending Aluminum Profiles
Two crucial factors determine the bending performance of aluminum profiles:
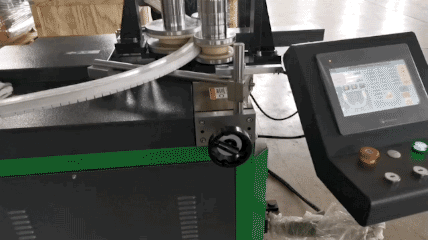
- Aluminum Alloy Elements
The bending performance of aluminum profiles mainly depends on their microstructure and the alloy elements’ content. Generally, adding alloy elements can significantly increase aluminum’s strength and hardness but also make it more brittle, which hinders bending. Therefore, it’s essential to select the appropriate strength and hardness based on the specific application needs.
Tip: You can refer to common aluminum alloy grades to understand their composition. Read more: - Heat Treatment State
The bending performance of aluminum profiles also relates to their heat treatment state and surface finish. Heat treatment alters the aluminum’s grain structure and stress state, improving its bending performance. Common heat treatments include annealing, solution treatment, and aging, which can significantly enhance bending capabilities. Surface treatments like spraying, anodizing, and electrophoretic coating typically improve corrosion resistance and surface hardness but have little effect on bending performance, which is generally negligible.
Tip: For parts with a challenging minimum bending radius, adjusting the heat treatment state can help. Read more:
Common Aluminum Alloys Used for Bending
Commonly used aluminium alloys include:
- Series 1xxx (Pure Aluminum): Known for excellent corrosion resistance and high ductility, these alloys are ideal for applications requiring minimal strength but maximum flexibility.
- Series 3xxx (Aluminum-Manganese): Offers good corrosion resistance and moderate strength, making it suitable for roofing, cladding, and other architectural uses.
- Series 5xxx (Aluminum-Magnesium): High strength and corrosion resistance make this alloy ideal for marine and automotive industries. It also demonstrates good bending properties, especially in annealed states.
- Series 6xxx (Aluminum-Magnesium-Silicon): Balancing strength, corrosion resistance, and excellent machinability, this versatile alloy is widely used in construction and transportation.
- Series 7xxx (Aluminum-Zinc): With superior strength and hardness, these alloys are suitable for aerospace applications but require careful handling during bending due to lower ductility.
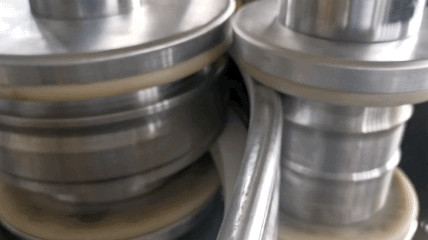
The commonly used aluminum alloys are 6063, 6061, etc., which are heat-treated to T5 or T6 states to enhance the mechanical properties of the profiles. These alloys are widely applied in various industries, including:
- Construction Industry: Doors, windows, curtain walls, sunrooms, handrails, partitions, etc.
- Transportation: Car frames, train carriages, aerospace components, bicycle frames, etc.
- Electronics and Electrical: Heat sinks, cable trays, electronic device housings, etc.
- Mechanical Manufacturing: Industrial frames, assembly line equipment supports, tool supports, etc.
- Consumer Goods: Furniture, household appliances, sports equipment, lighting fixtures, etc.
Aluminum Bending Processes
There are various forms of aluminum bending processes, with two main classification methods:
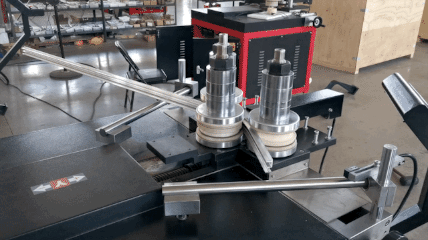
Bending Temperature
The process of bending at room temperature is known as cold bending, which doesn’t require additional heating of the material.
Bending that occurs when the metal reaches a certain high temperature is called hot bending. It typically requires heating the metal above its plastic deformation temperature.
Due to the limited plasticity of aluminum profiles at room temperature, cold bending may be challenging for complex shapes with smaller radii. Hot bending, however, can accommodate a wider range of materials and easily achieve smaller radii bends.
Key Point: Cold bending is the preferred process for aluminum bending due to its wide application range and stable forming.
Read more:
Why Choose Cold Bending for Aluminum?
Aluminum Bending: Choosing and Calculating the Minimum Bending Radius.
Bending Methods
There are various mechanical principles for aluminum bending, with the most commonly used being roll bending and stretch bending. In fact, there are many other methods for forming aluminum parts, such as the following 8 bending processes:
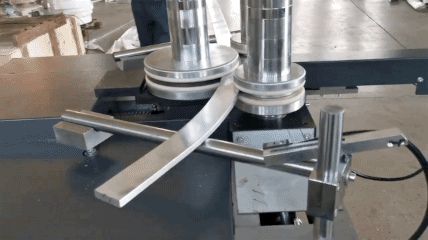
- Ram/Push Bending
- Rotary Draw Bending
- Compression Bending
- Free-Form Bending
- Press Brake Bending
- Hydraulic Press Bending
- Fluid Cell Press Bending
- Hand Bending
Read more: How to Choose the Right Bending Process for Aluminum?
7 Steps for Bending Aluminum Profile
- Incoming Material Inspection
Inspect profile cross-sectional dimensions, straightness, blank length, and surface quality. Pay special attention to any surface defects. - Milling
For reverse T-shaped frames, mill the profile cross-section before bending to ensure post-bending dimensions meet specifications. - Pre-Bending
Conduct pre-bending tests on CNC aluminum bending machines to achieve the desired pre-formed shape:- CNC Aluminum Roll Bending Machines: Set roll bending parameters or import drawings for pre-bending. Adjust based on spring-back to achieve optimal results. For the PBA series aluminium bending machines, the CNC system calculates compensation coefficients based on the actual radius, completing the process efficiently.
- CNC Stretch Bending Machines: Use stretch bending molds and clamps to pre-stretch blanks by controlling parameters such as stretching force and bending angles to meet pre-forming requirements.
- Trimming
Verify the flatness and angles of both surfaces, ensuring they meet the required specifications. In stretch bending processes, pre-bending can assist in fine-tuning the R-value to achieve the desired shape. - Inspection After Pre-Bending
Check the flatness, angles, and cross-sectional width of the profile to ensure compliance with specifications. - Mass Production
Proceed with mass production using pre-bending parameters established during testing. - Final Inspection
Use inspection molds along with calipers and feeler gauges to verify that the final products meet technical and drawing requirements specified by the customer.
Conclusion
Aluminum profiles possess excellent bending performance, but their specific bending capabilities depend on factors like alloy composition, microstructure, surface treatment, and heat treatment state. When bending aluminum profiles, it’s crucial to select the right material based on the specific application needs and process requirements. Understanding the proper aluminum bending techniques ensures high bending performance and quality.