The bending radius is a key parameter in aluminum bending, directly affecting the quality and precision of the process. This article highlights the principles of bending aluminum, the factors influencing the bending radius, and how to select and calculate the radius using advanced aluminum bending machines.
Principles of Bending Aluminum
Bending aluminum involves using mechanical force to shape profiles into specific arcs. During this process, the material undergoes stretching, compression, and shearing, resulting in plastic deformation that creates the desired curve. High-performance aluminum bending machines ensure precision and consistency throughout the process.
Key Factors Influencing the Bending Radius
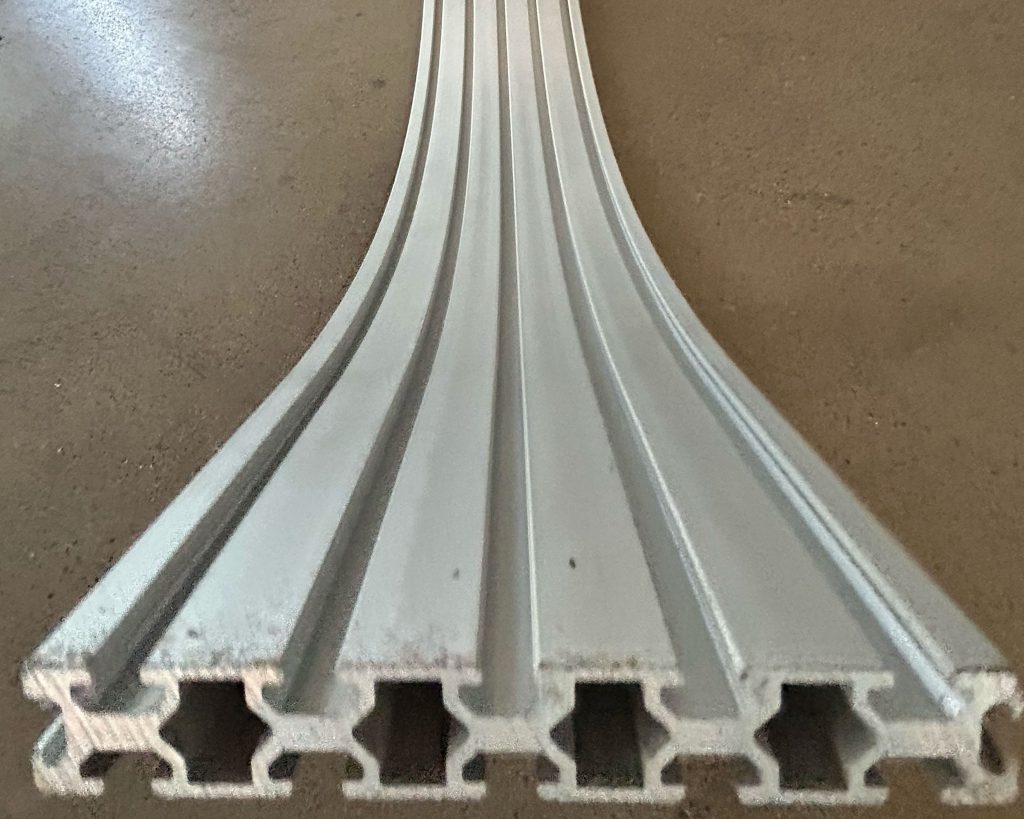

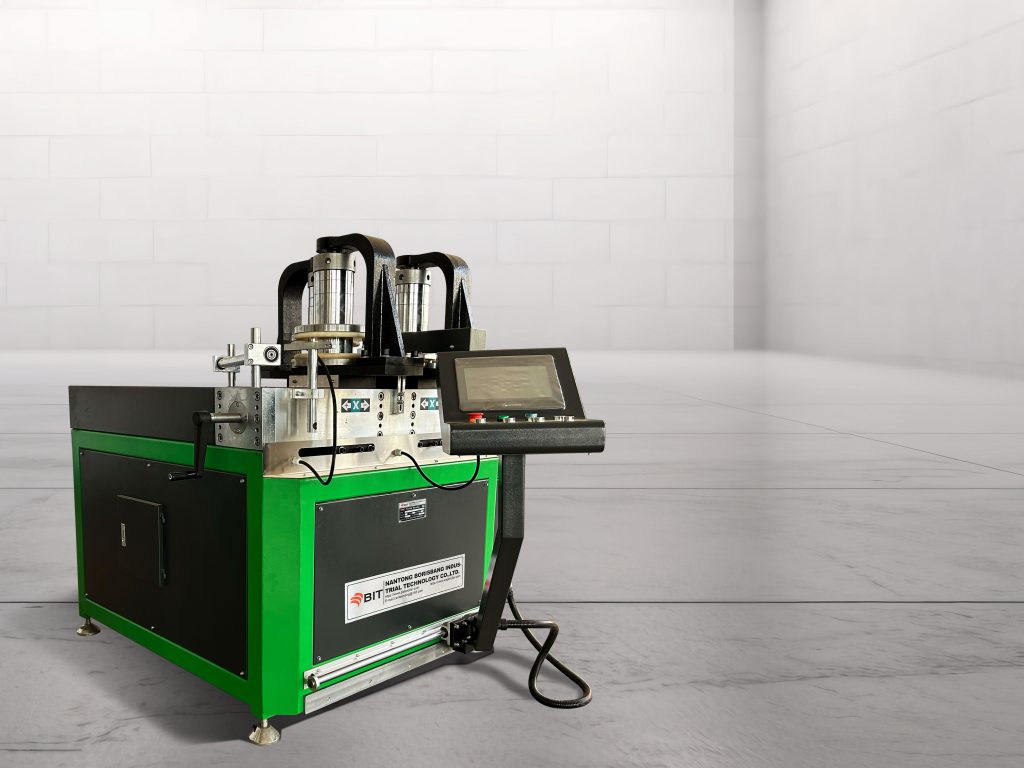
- Material Properties
Aluminum’s strength, hardness, and plasticity determine how easily it bends. Softer alloys allow tighter radii, making them ideal for complex shapes. - Profile Dimensions
Larger diameters and thicker walls enhance rigidity, allowing smaller bending radii without compromising structural integrity. - Bending Angle
Larger angles require tighter radii but may increase the risk of cracking. Choosing the right angle ensures smooth transitions. - Bending Speed
Slower speeds improve precision, as they allow the aluminum more time to deform evenly. - Aluminum Bending Machine Precision
Advanced machines with high accuracy enable tighter radii, better control, and fewer defects during the bending process.
Selecting and Calculating the Bending Radius
- Basic Principles
The bending radius should typically be at least 1.5 times the profile diameter to balance flexibility and strength. - Empirical Formula
Use R=K×DR = K \times DR=K×D, where RRR is the radius, DDD is the diameter, and KKK (1.5–2) is an empirical factor based on material properties. - Simulation Tools
Modern aluminum bending machines use software to simulate bending processes, ensuring optimal radius selection based on material and profile characteristics.
Online Bending Radius Calculator Easily estimate recommended and theoretical bending radii based on your profile width and orientation (easy or hard way). This tool helps prevent cracking, wrinkling, and shape deformation before bending begins. 👉 Try the calculator now
Conclusion
Achieving precise aluminum bending requires selecting the right bending radius. By analyzing material properties, dimensions, and equipment capabilities, manufacturers can enhance quality and efficiency. Advanced aluminum bending machines simplify the process, providing reliable results and minimizing errors.
In summary, focusing on the bending radius ensures high-quality outcomes, making bending aluminum a precise and efficient operation.