There are many advantages to bending angle aluminum. Angle aluminum is light and strong, and it still maintains high strength after bending, which is suitable for occasions where weight reduction is required. An oxide film will form on the surface of aluminum, making it less prone to rust and suitable for outdoor or humid environments. Angle aluminum is easy to cut, drill and bend, and is suitable for processing complex shapes. The bent angle aluminum can be used for decorative structures, and the surface can also be treated in various ways, such as anodizing or spraying, to look more beautiful. Finally, aluminum can be recycled and meets environmental protection requirements.
Bending Process
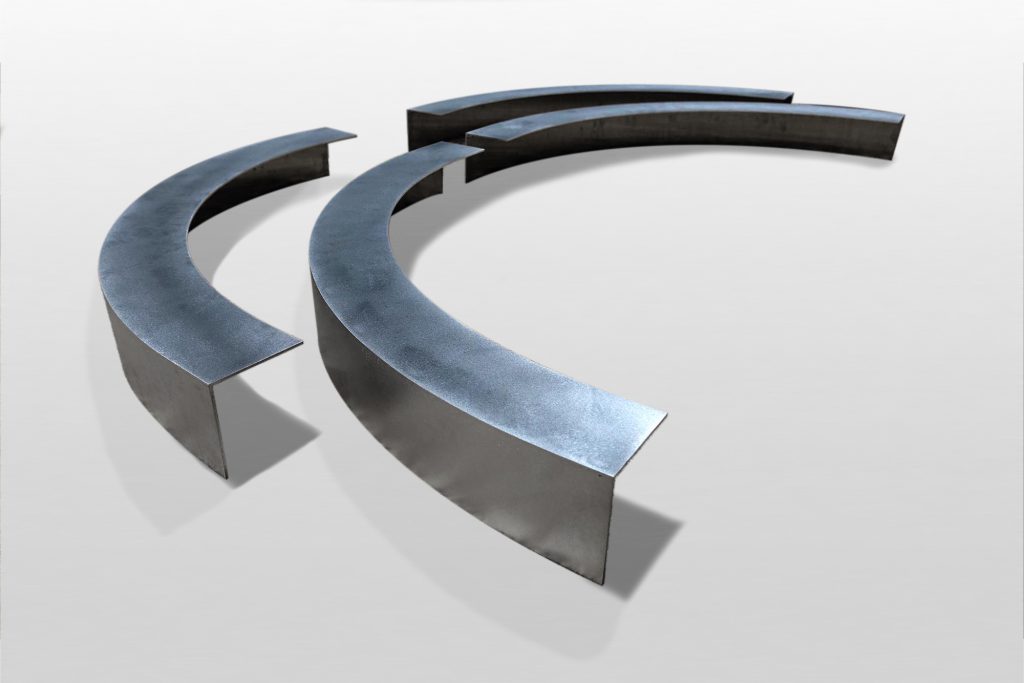
Angle aluminum bending is a process that can bend angle aluminum into shape through a variety of machines. Since angle aluminum is L-shaped, it is more complicated to bend than flat plates or round tubes.
Rolling is one of the best choices for angle aluminum. Our PBA aluminum profile bending machine can slowly bend angle aluminum into an arc, which is suitable for large radius bending and high-precision batch repetitive production. For example, when making curved door and window frames or curtain wall supports, PBA aluminum bending machines are an efficient choice.
There are two bending directions for angle aluminum:
- Leg bending outward means that the vertical leg bends outward to form a smooth arc, which is often used for flanges and decorative structures.
- Leg bending inward means that the vertical leg bends inward to form a compact arc, which is suitable for mechanical parts and supporting structures.
Since the angle aluminium is L-shaped, the cross-section of the aluminum profile is easily distorted when bending, so it is very important to control the deformation. The angle aluminum can be fixed by using guide rollers and customized special devices or polymer materials, bending in multiple times, gradually adjusting the shape, and selecting a suitable bending radius to avoid excessive deformation. In addition, whether the surface of the angle aluminum is anodized or not, we need to pay attention to protecting the surface from scratches during the bending process, to protect its aesthetics and corrosion resistance, so nylon is usually selected in the roller material. After bending, the corrosion resistance and aesthetics of the angle aluminum can be further improved by surface treatment methods such as anodizing or spraying.
Precautions
When bending aluminum and steel, one of the biggest differences is that material selection is very important. Choose the right aluminum alloy type, such as 6061, 6063 or 6082, according to the application to ensure strength and corrosion resistance after bending. 6061 aluminum alloy has high strength and is suitable for occasions requiring high stability; 6063 aluminum alloy is suitable for general processing projects; 6082 aluminum alloy is often used in occasions with medium strength requirements such as bridges and cranes.
Steel Angle vs. Aluminum Angle
Property | Steel Angle | Aluminum Angle |
---|---|---|
Strength | Higher strength, ideal for heavy loads | Lower strength, but lightweight |
Weight | Heavier | Lightweight |
Corrosion Resistance | Prone to rust, requires coating | Naturally corrosion-resistant |
Cold Weather | Can become brittle | Maintains ductility in cold temperatures |
Weldability | Easier to weld | Requires precision welding |
Cost | Generally cheaper | More expensive |
Aesthetic Use | Rarely used for decoration | Commonly used for decorative purposes |
Fabrication | Harder to machine, produces sparks | Easier to machine, no sparks |
Applications | Heavy-duty structures, construction | Lightweight structures, outdoor use |
Aluminum is very hard in the T6 state, and direct bending may cause fracture. To solve this problem, the state of the aluminum can be changed by heating to make it easier to bend. Alternatively, you can choose T4, T5 and other states for bending, and then perform aging hardening after bending to restore the strength of the material.
The choice of bending radius is also critical. Avoid too small a bending radius, otherwise the angle aluminum may crack or deform. To avoid this, you need to choose a suitable bending radius based on the thickness of the material and the bending requirements. Generally, a larger bending radius can reduce the risk of surface wrinkling.
Controlling deformation is another important link. Special clamps or guide rollers can be used to prevent twisting or warping during bending. Equipment selection is also very important. Choose the right equipment according to the bending requirements, such as a rolling machine or a bending machine, to ensure processing accuracy. Finally, after bending, pay attention to protecting the surface of the angle aluminum to