The stretch forming process applies tension and bending moment at both ends of the tent profile, so that the aluminum tent profile is stretched and bent while wrapped around the forming die. This can effectively reduce the bending rebound and improve the contour accuracy of the tent profile. It is particularly suitable for the bending forming of tent profiles with small deformation and large curvature radius.
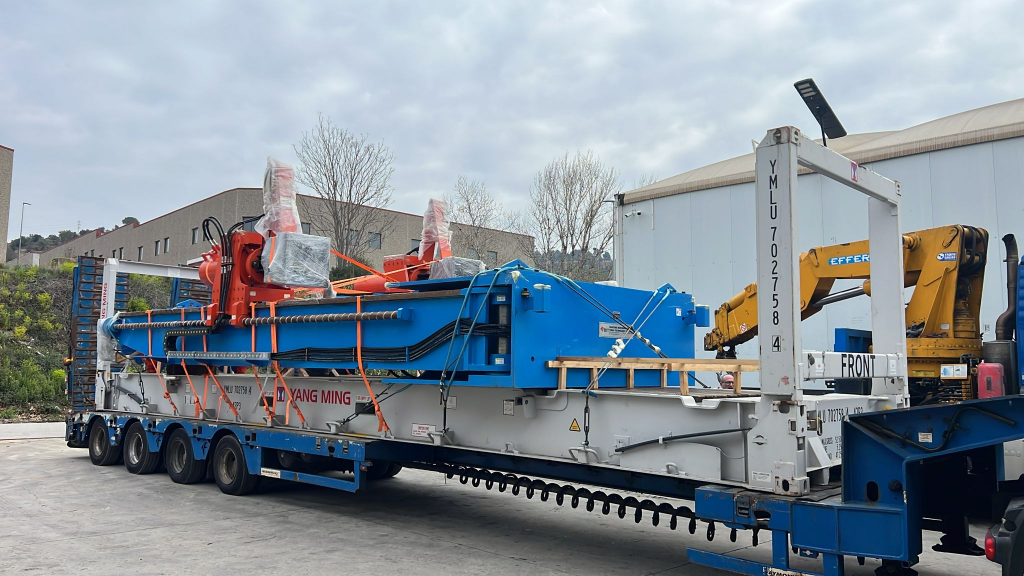
Tent profiles often have large cross-sections, requiring careful selection of bending methods. For profiles wider than 200mm, using a stretch forming machine ensures high precision and minimizes deformation and springback. For profiles under 200mm, an aluminum profile bending machine is a suitable option, though material condition remains crucial. Typically, T4 or T5 aluminum profiles are ideal for bending, as their moderate hardness helps reduce springback and maintain shape.
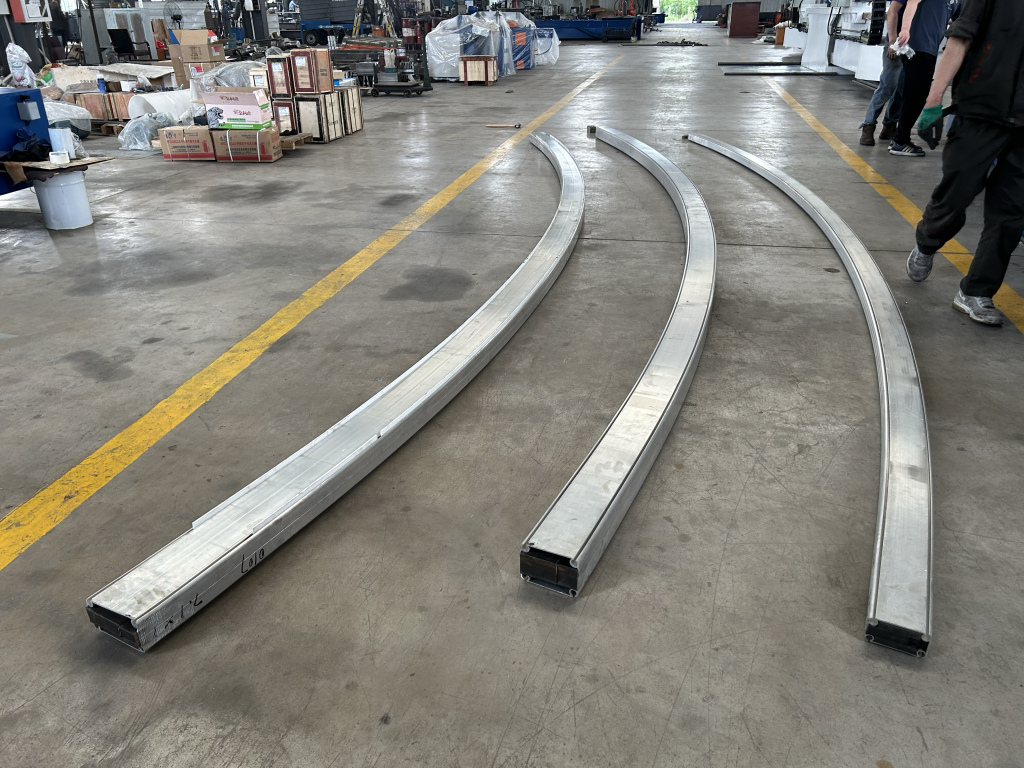
A stretch forming machine provides excellent shape control for tent profiles, preventing surface wrinkles and inner-side dents. This method is particularly beneficial for large, variable-radius aluminum profiles, ensuring consistency while reducing post-processing adjustments. In contrast, an aluminium profile bending machine is more efficient for small cross-sections but offers lower precision.
During processing, challenges include shape deviation, surface defects, twisting, and vertical misalignment. Shape deviation, often caused by uneven hardness or springback, can be corrected by optimizing die curvature and adjusting tension. Surface defects may result from excessive force, profile design, or die clearance, requiring careful parameter adjustments. Twisting can be minimized by increasing tension and modifying front-end die support. Vertical misalignment can be corrected through appropriate compensation techniques.
The blank length of the tent profile should fully consider factors such as the length of the part, the extension of the mold curvature, the clamping part of the equipment chuck and the rotation gap between the equipment chuck and the mold. Under the premise of meeting the requirements of the tent profile forming, the process margin should be minimized to reduce the cost.