Roll bending of steel structural profiles and aluminum extrusion profiles differs significantly in material properties, process control, and equipment requirements. These differences directly impact the bending force selection, deformation behavior, and precision control.
Material Properties
Steel structural profiles have higher strength and yield points, requiring greater bending force. In contrast, aluminum extrusion profiles are softer and easier to bend, but they exhibit greater elastic recovery, requiring compensation for springback. Steel has excellent plastic deformation capability, making it less prone to fracture during bending, with minimal springback. In comparison, aluminum has higher elasticity, leading to more noticeable springback, especially in 6000 and 7000 series alloys.
Regarding fracture risks, steel profiles typically do not fracture during bending but may become brittle at low temperatures, leading to potential brittle fractures. Aluminum profiles, however, are prone to surface cracks, especially in thin-walled sections or high-alloy materials.
Roll Bending Process
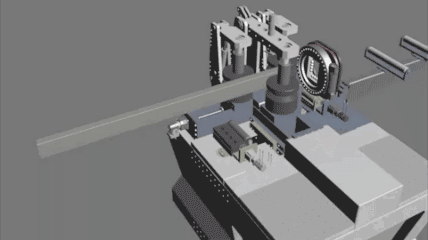
Steel profile roll bending requires high-strength, wear-resistant rollers, typically made of alloy steel to withstand high pressure. Aluminum profiles, on the other hand, require smooth rollers (such as nylon rollers) to prevent surface scratches.
For feeding and pressure control, steel profiles require higher hydraulic or mechanical force, often using multiple passes to gradually increase bending depth, preventing fracture or excessive deformation. In contrast, aluminum profiles require pre-bending and compensation bending to improve accuracy, along with precise pressure control to avoid surface defects or local collapse.
Pre-bending and compensation play different roles: in steel, pre-bending mainly ensures uniform transition at the bending start, while in aluminum, pre-bending and compensation are crucial due to significant springback. Aluminum profiles often require post-bending adjustments to eliminate springback errors.
Equipment and Precision Requirements
Steel profile roll bending requires high-rigidity machines with stronger hydraulic systems, while aluminum profiles demand higher precision control systems to minimize deformation.
For profile bending machine control, steel profile bending typically uses traditional hydraulic control, though CNC systems are sometimes used for high-precision applications. In contrast, aluminum profile bending relies more on CNC systems combined with simulation software to predict and compensate for springback.
Deformation Control and Correction
For steel structural profiles, common deformation issues include warping, twisting, and section instability. Solutions include:
- Multi-point support to prevent section deformation due to concentrated bending force.
- Controlled feed rate to avoid local stress concentration from excessive force application.
- Pre-compensation for welding deformation in large-span structures.
For aluminum extrusion profiles, common issues include springback, collapse, and surface damage. Solutions include:
- CNC-calculated springback compensation for higher accuracy.
- Internal filler tooling to prevent profile collapse during bending.
- Optimized surface contact, using coatings or soft contact materials to reduce friction and scratches.
Conclusion
Although steel and aluminum profile roll bending processes share similarities, significant differences arise due to material properties. Steel profiles have high strength, good plasticity, and minimal springback, making control relatively simple. Aluminum profiles, with higher elasticity and significant springback, require more precise control and compensation.